Arvato wprowadza nowoczesne robotyczne rozwiązanie wspomagane sztuczną inteligencją
02 lipca 2024
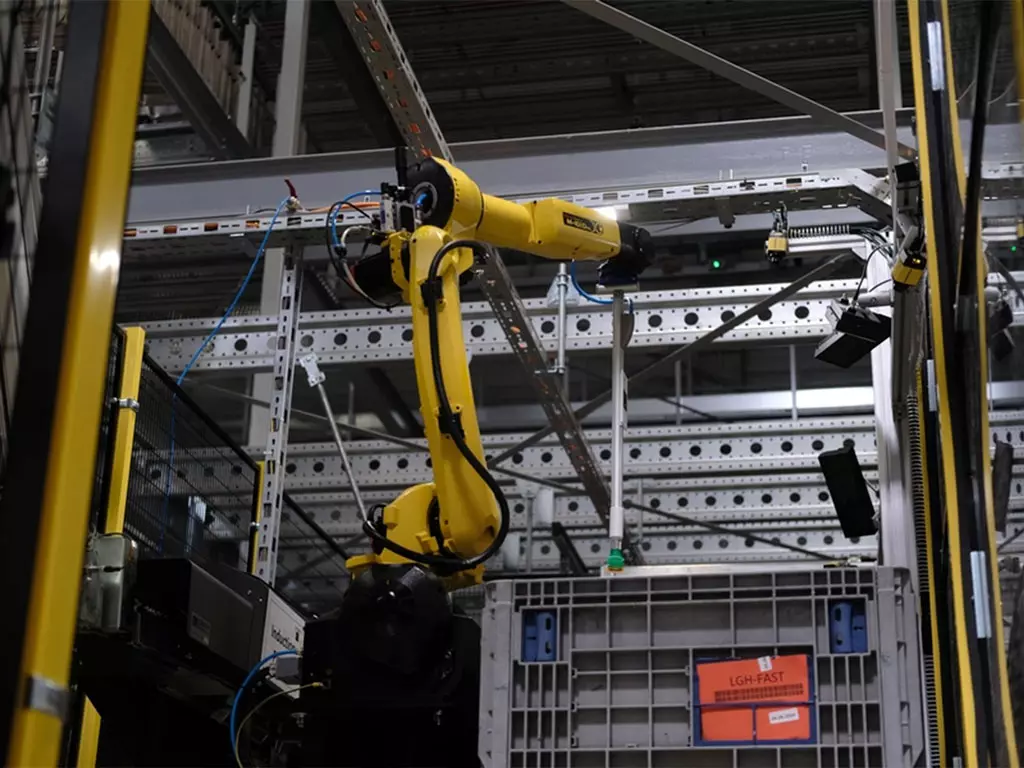
Spis treści
Robot wykorzystuje zaawansowane systemy wizyjne oparte na sztucznej inteligencji, aby zautomatyzować proces rozładowywania pojemników zbiorczych, w których znajdują się setki sztuk odzieży. Wysoka precyzja i dokładność podejmowanych decyzji gwarantują niezawodność i efektywność wykonywanych zadań.
W ramach integracji z systemem BagSorter robotyczne ramię identyfikuje optymalne miejsce do uchwycenia każdego produktu, co zapewnia bezpieczny i efektywny ruch. Lelka sprawdza widoczność produktu, jego pozycję w stosunku do innych oraz czytelność kodów kreskowych, skutecznie radząc sobie z nieregularnie ułożonymi produktami losowo w pojemnikach.
Leleka przejmie żmudne zadania
Głównym celem wdrożenia Leleka było odciążenie pracowników od najbardziej monotonnych i żmudnych zadań, takich jak przenoszenie produktów w magazynie. W miarę wzrostu wolumenu pracy coraz trudniej jest zatrudniać nowych pracowników do podstawowych procesów logistycznych. Leleka, wyposażona w algorytmy AI oparte na przetwarzaniu obrazu, została zaprojektowana do obsługi skomplikowanych zadań z wyjątkową precyzją, co poprawia jakość operacji.
– Leleka oferuje długoterminowe korzyści finansowe, odpowiada na braki kadrowe i odciąża pracowników poprzez automatyzację rutynowych zadań. Zwiększa stabilność i efektywność operacyjną, wspierając procesy logistyczne Arvato nawet przez całą dobę – mówi Sławomir Grzeskowiak, szef zespołu R&D Arvato.
Zautomatyzowane funkcjonowanie
Leleka jest świetnym przykładem wykorzystania zalet AI w logistyce. Robot osiąga wydajność porównywalną z ludzką, ale bez obniżenia produktywności z powodu zmęczenia. System jest zoptymalizowany do pracy przez całą dobę, 7 dni w tygodniu, zapewniając ciągłość operacji. Działa autonomicznie, wymagając minimalnej interwencji pracowników przy wymianie pojemników zbiorczych, choć planowana jest automatyzacja również tego procesu.
– Rozwój Leleka stanowił znaczące wyzwania, szczególnie w zderzeniu teorii z rzeczywistością. Produkty, nigdy nie są idealnie ułożone w pojemnikach zbiorczych, co wymagało dostosowaniu się do nowych warunków w oparciu o wiele kryteriów. Dzięki rygorystycznym testom i adaptacji rozwiązania do istniejących warunków nasz zespół projektowy pomyślnie sprostał tym wyzwaniom, zdobywając cenne doświadczenia i ogromne ilości danych do przyszłych wdrożeń – wyjaśnia Grzeskowiak.