Omnichannel in a warehouse. The first mile equally important as the last one
15 december 2019
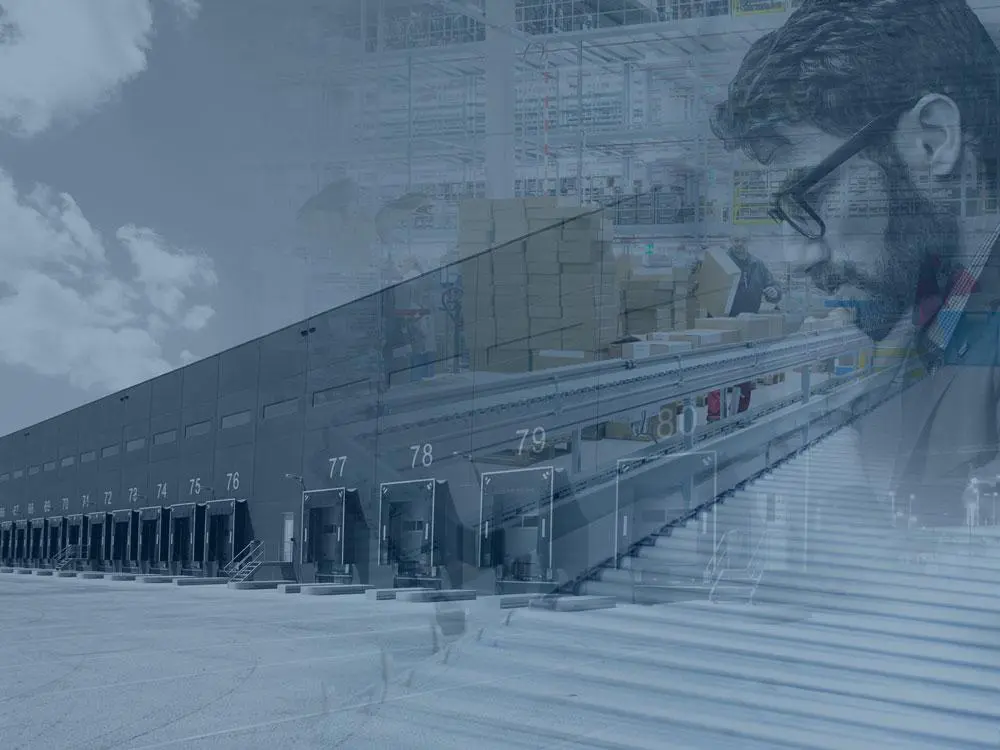
Contents
Equally important is the correct product acceptance that begins with an order entering the WMS and is actually the first part of the entire order fulfilment process. The first mile remains underestimated in product deliveries to a store or an end consumer, but plays an increasingly important role.
Polish customers are among the most discerning European consumers as regards delivery times and places. Recent research has revealed that 57% of customers shop both online and offline, but the proportion of online and offline buyers of home appliances and electronics already stands at 71%.
As the proportion of omnichannel customers is growing and large warehouse sizes are required to operate several sales channels, an appropriate design of warehouse space is becoming a critical issue. Acceptance, storage, picking and release of orders for several channels may require up to three times the size of a traditional warehouse. This is mainly due to such reasons as:
- the need for quick delivery acceptance and making goods available for sale,
- swift order picking requirements,
- the inevitability of large fluctuations in line with seasons, holidays and sales periods, and
- the need for separate additional zones to accommodate customer requirements and create the right customer experience.
Logistics - source of competitiveness advantage
Due to all the above requirements, a traditional warehouse with pallet racks is unlikely to meet occupier requirements. It is critical that companies realise that logistics should be treated as a means to gain a competitive advantage rather than a cost. That’s why having a warehouse that meets special requirements is becoming an essential part of market strategies of omnichannel retailers.
In terms of operational performance, an ideal e-commerce warehouse should have the following:
- an appropriately-designed zone for acceptance and release of goods that could be adjusted depending on the volume of deliveries and shipments,
- various storage zones (pallet and shelf racks, clothing racks). Such systems should enable easy transfer or relocation of products within and between zones, e.g. during changes of seasons or during sales and promotions,
- dedicated product storage systems (e.g. single- and multi-SKU locations, chaotic storage, zone storage),
- a zone with value-added services (labelling, co-packing, picking promotional sets),
- a shelf zone for leaflets, supplements and samples added to parcels in a packing zone,
- a return processing zone,
- a sorting zone,
- a buffer zone for picked orders waiting to be handed over to a courier company,
- a storage zone for packaging materials.
Jak efektywnie wykorzystać powierzchnię magazynową?
Aby jak najefektywniej wykorzystać powierzchnię magazynową, coraz częściej spotyka się antresole, zawierające np.:
- multilayer cardboard shelf racks,
- metal racks with plastic containers for picking small items,
- mezzanine lifts,
- conveyor belts sending picked goods to packing zones, etc.
- top-quality packing and returns management zones, or zones for picking promotional sets.
A mezzanine enables a more efficient adaptation and optimum adjustment of available space to individual needs and warehouse conditions. Its construction sometimes requires an adequately reinforced floor, more efficient ventilation systems and appropriate lighting, especially in spaces for regular work in packing and return processing zones.
In line with legislation, appropriate lighting must be ensured in places where a single person spends more than four hours a day. Buildings featuring order picking zones with additional lighting in excess of the minimum standard of 300 lux are being constructed more and more often. Mezzanines also need to meet stricter firefighting requirements and be equipped, for instance, with additional sprinkler systems.
Zalety obiektów BTO i BTS
Poland has seen BTO (build-to-own) and BTS (build-to-suit) warehouses delivered to the market in the last few years. They are tailor-made facilities and are frequently higher than standard schemes, providing additional spaces measuring up to 18 metres in height to accommodate multi-level pick-towers for efficient and integrated processing of multiple orders at the same time.
Due to a high number of staff required to process orders, companies are increasingly focusing on providing suitable welfare spaces, including comfortable locker rooms with modern sanitary facilities, as well as spacious canteens, conference rooms and chillout rooms. Ample parking spaces for employees are also essential. As their availability is frequently limited by the size of a car park and the need to provide spaces for trucks and swap bodies, employers tend to cover travelling costs, arrange bus services and contribute to car-sharing expenses.
Omnichannel has its requirements
Doors and docks are also key features of an appropriately designed warehouses for omnichannel retailing. Some warehouses of this type need to provide an above-standard number of grade-level doors to meet the requirements of product ranges and sizes. However, if a tenant expects to sign agreements with several courier companies which will be collecting parcels in similar time slots, several grade-level doors will have to be fitted.
Learn more about last mile logistics - download the "Last Link: Quantifying the cost" report!