What to consider in planning a pharmaceutical warehouse?
19 july 2022
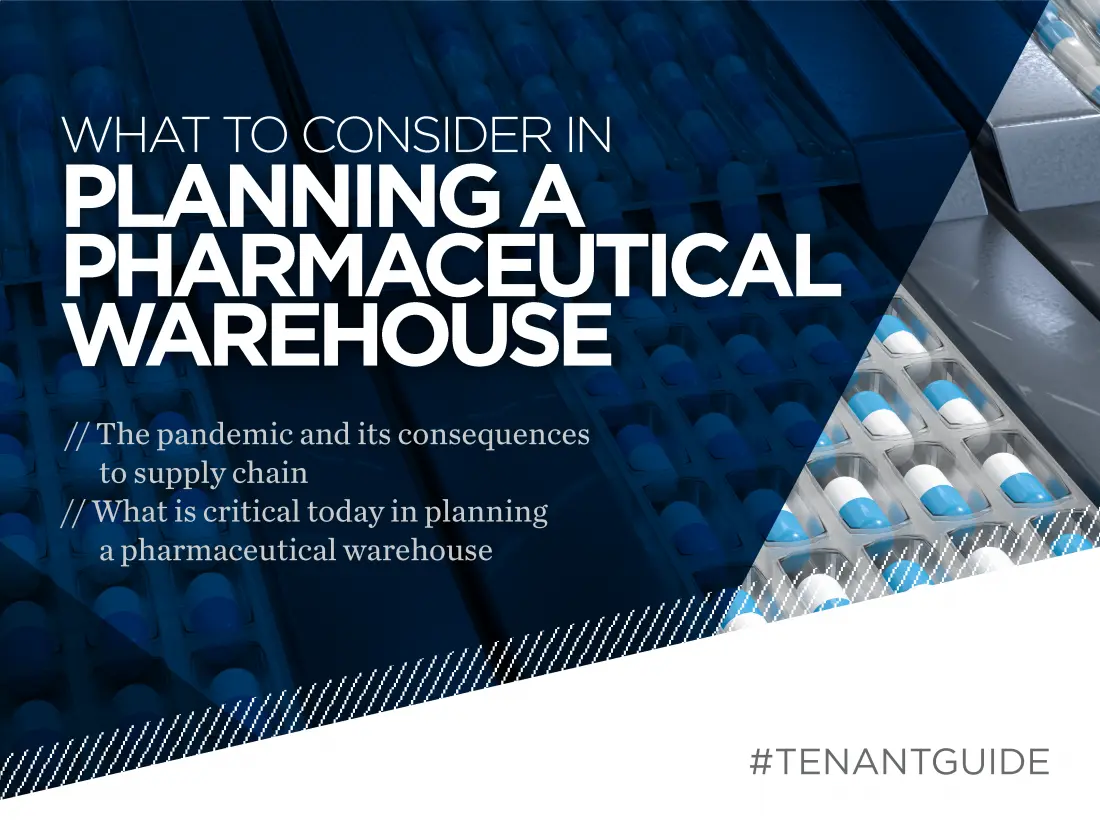
Contents
Pharmaceutical logistics continues to grow at pace, largely fuelled by the pandemic, with global governments around the world now emphasizing ample medicinal supply for patients. Its growth is also attributed to the increasing demand for OTC preparations, from vitamins through to dermatology products.
According to Grand View Research, the global pharmaceutical logistics market was valued at USD 78.5 billion in 2021 and is expected to advance at a compound annual growth rate of 8.6% by the end of 2030 to reach USD 163.9 billion during the forecast period of 2022-2030.
The pandemic has laid bare the consequences of supply chain disruptions and the lack of manufacturing diversification. Ensuring continuity of medicinal supplies for patients has become critical. Key to this process is a facility for storing, manufacturing and packaging of medicines.
Preparing a warehouse for pharmaceutical operations
To be safe and efficacious, drugs and other pharmaceutical products require specialist warehouses meeting the highest standards and featuring special improvements. That is why it is so important to properly analyse and plan a warehouse project and its intended functions at the start of the development process. The best solution in the case of a pharmaceutical warehouse would be to consider leasing a BTS project or space in a multi-let facility whose construction is just about to commence and which can be customized while it is still being designed.
Division of warehouse zones
In practice, pharmaceutical buildings feature separate areas, including reception/dispatch areas, laboratory space, clean rooms, manufacturing space and storage space. Rounded wall/floor junctions make for easy cleaning. UV lamps help sanitize rooms. Pharmaceutical logistics frequently requires a cold chain, or distribution, transport and storage of goods at a constant and controlled temperature. The ambient temperature in pharmaceutical warehouses is expected to be in the range of +15°C to +25°C. As a result, new build facilities should enable a rigorous control and maintenance of the right air temperature, which in turn requires proper building insulation. This should be no big challenge in new buildings as designers of modern warehouses continue to think of new technological solutions aiming at achieving a carbon neutral status, with such facilities significantly exceeding predefined technical specifications. That being said, handling temperature-sensitive products will require a range modifications to warehousing operations and obtaining prior approvals from a Provincial Pharmaceutical Inspectorate (WIF) and the Chief Pharmaceutical Inspectorate (GIF).
The method of stocking pharmaceutical products
The primary requirement is to ensure a temperature in the range of +15°C to +25°C, which is enabled by precision air-conditioning adapted to racking systems and the ductwork distributing airflow throughout a warehouse. Following receipt of goods it is necessary to segregate operations into receiving/dispatch bays and - in some cases - also into an area for quarantined pharmaceutical products. This is enabled by panel walls - mostly full-length - and high-speed doors facilitating the movement of forklifts throughout the warehouse. In addition to dedicated office space, most warehousing operations will require cold storage areas for products to be kept at lower temperatures, premises for flammable materials such as aerosols, premises for psychotropic drugs with additional anti-burglary protection or premises for repacking drugs (commonplace in Poland on account of supply chain diversification).
Special demand for pharmaceutical industry warehouses
Standard warehouses delivered by developers in Poland usually need to be adapted to meet these requirements. The BTS formula adopted at an early stage of development allows for adapting planned processes to each type of operations within a very short timeframe and avoiding the costs of redeveloping existing space.
Key points to remember:
- backup power supply (a power generator);
- reinforced rooftop structure for air handling units;
- adaptation of external areas to various means of transport, including electric vehicle charging stations;
- loading docks with seals and PVC strip curtains or additionally - for more demanding products - positive pressure of 15-25 Pa to prevent insects from getting inside;
- HCCP / non-breakable fixtures, washable walls and vertical cladding;
- washable paint on the building’s walls and structural elements;
- designated battery charging areas with hoods in an explosion-proof design, hydrogen sensors, and epoxy floors;
- adaptation of the building’s fire-fighting system to individual areas, and of the air supply and smoke removal system;
- canopy roofs over grade-level and entrance doors;
- temperature control with recorders and automatic alerts to maintenance services when the temperature nears a danger level; and
- mezzanines – multi-level racking systems.
What is critical today is that supply chains are secure and manufacturers produce pharmaceuticals as close to the target consumers as possible. As patients’ demand for the fastest delivery possible continues to grow, development activity will increasingly focus on projects tailored specifically to the requirements of the pharmaceutical industry.