How to prepare for a change of warehouse location?
07 july 2020
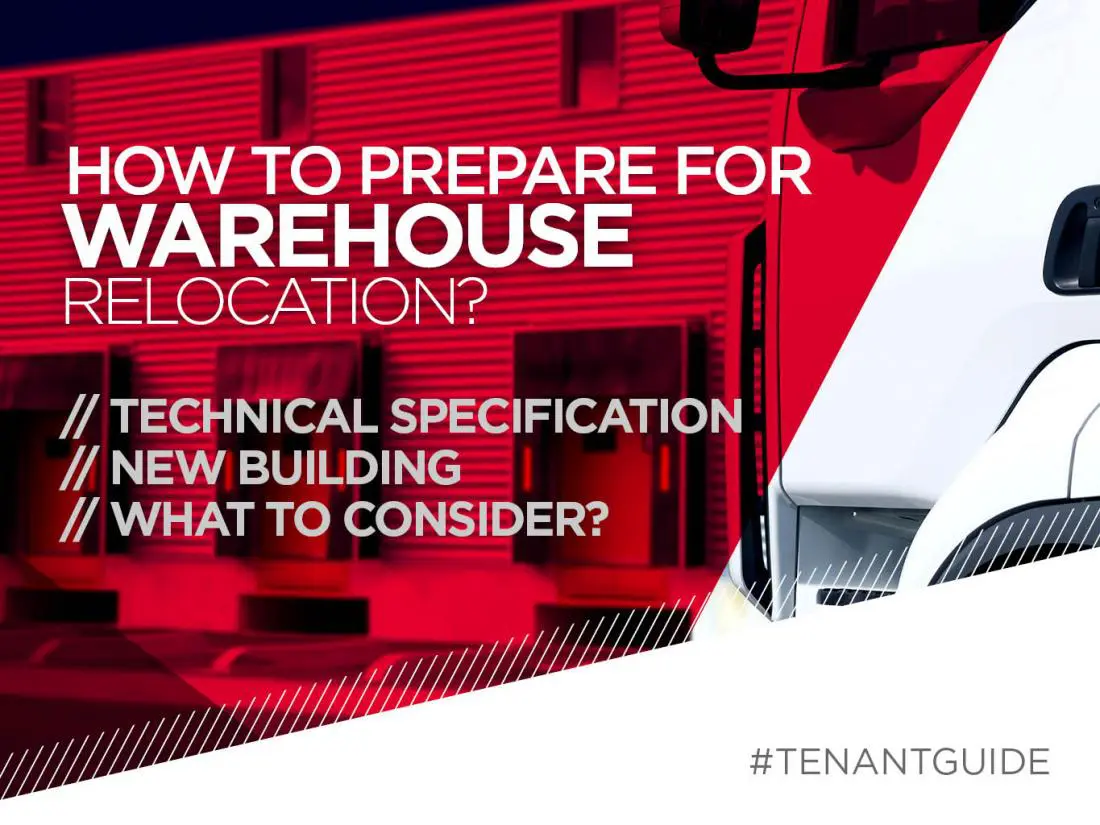
Contents
Once you’ve made a decision to move to a new logistics location, you need to begin making appropriate preparations right from the outset of the process. How to ensure that everything runs as expected?
All the steps of the relocation process must be carefully thought out so that the choice of a new place, lease negotiations and construction happen as expected and are under your control.
When you set about choosing a new logistics location, right at the outset you should specify what type of warehouse you expect and what technical specifications it should meet so that you are able to move into a bespoke building once it is delivered.
Technical specification of a warehouse. What should it include?
Developers are able to deliver a new logistics facility under a turnkey model, but they need to know the requirements they have to meet. Such requirements must be set out in a technical specification which - in addition to the location and the start date of operations in the new facility - is one of the key elements of a request for proposals sent out to developers.
The technical specification should include the following:
Dimensions of a warehouse
(powierzchnia, wysokość, siatka słupów, podział na strefy, itp.).
Dimensions of a warehouse
(area, height, column grid, division into zones, and so forth).
Dimensions and the fit-out standard
of an office and welfare building (area), number of employees and shifts, type of locker rooms, and so forth – these data will enable developers to exactly specify the area of office and welfare facilities and the fit-out standard. Offices are currently built to good standard (air-conditioning, wall-to-wall carpet finish), but some tenants report requirements in excess of what is provided by developers as standard.
Types and quantities of dangerous goods (ADR)
that will be kept in the warehouse, and storage methods. Dangerous goods require an appropriately prepared building that should be fitted with adequate fire-extinguishing systems. Inclusion of information on dangerous goods is also important for formal reasons as standard lease provisions prohibit storage of dangerous goods unless otherwise agreed with the developer in a lease agreement;
Whether a mezzanine is planned to be constructed
in a building and its specification details such as the number of levels and employees. This is important due to the complicated procedure of obtaining design approvals and building permits for a mezzanine. In addition, a building’s systems including sprinklers, ventilation and lighting must be adapted to the mezzanine – such systems are much easier and cheaper to take account of at the design stage and to build before the building is completed (e.g. capacity of the fire-fighting system).
Maximum floor load, levelling and flatness requirements
The standard floor load is 5 tonnes per sq m. However, the floor load capacity must be higher wherever there are plans for mezzanines or high pick towers, including the use of stackers – usually for up to 10 tonnes per sq m. A level and flat floor is especially important for stackers on account of their high lifting heights and speed of operation, and any floor deviations will pose a risk to pick towers and the building itself.
Expected temperature inside a warehouse
Depending on the planned inside temperature, suitable materials for building envelopes such as external walls and roofs must be selected. Under Polish legislation there are various heat transfer coefficients that depend on the planned temperature inside a building. The standard temperature in warehouse buildings is +15 degrees Celsius (the heat transfer coefficient for temperatures below 16 degrees Celsius). However, for instance, on account of the nature of warehouse operations, a higher temperature may be required – with higher heat transfer coefficients recommended for temperatures above 16 degrees Celsius. The planned temperature should be specified in a request for proposals sent out to developers as any change to the thermal performance of building envelopes is virtually impossible and very costly once the building is completed. On the other hand, building envelopes with inappropriate heat transfer coefficients may result in higher service charges.
Refrigeration
If a refrigeration system is to be provided by a developer, features that need to be specified include a refrigerant, the number and size of cold rooms and temperature ranges, as well as required temperature monitoring systems. All this will have an effect on service charges borne by tenants. For instance, electricity consumption with carbon dioxide (R744) and ammonia (R717) is approximately 40% and 30% lower than with the standard HFC (R404a), respectively.
Sustainability. If a new building is to feature sustainable solutions, they should be included in technical specification. As BREEAM and LEED certification of logistics buildings is not standard practice yet, it is important that relevant certification requirements be specified.
A precise technical specification submitted to a developer with a request for proposals will enable the developer to estimate the costs of construction of a bespoke building for the tenant in a lease offer more precisely. In the case of an imprecise technical specification or lack of it, the developer will generally provide estimated adaptation costs, as a result of which the lease offer may fail to meet the tenant’s expectations.
Warehouse construction costs vs technical specification
A well-prepared and precise technical specification also constitutes a technical attachment to a lease agreement (with plot and building layouts) and will be used by the developer as reference material to prepare a detailed design of a building.
Advantages of a well-prepared technical specification:
- an optimum lease offer for a building delivered in line with the tenant’s expectations,
- comparison of lease offers based on identical sets of data submitted by developers taking part in a tender,
- limited risk of change requirements (delays and additional costs) after the lease is signed, during the design and construction stage.
To sum up, precise specification of occupier requirements at an early stage of relocation generates a heavier workload initially, but will enable the developer to deliver a building meeting the tenant’s expectations and reduce the risk of any delays and unforeseen costs during later relocation stages.
Find out more about the BTS and BTO type investments here.